What is SAP MM (Material Management)
SAP Materials Management (MM) provides inventory and material control. This module manages resources and inventory levels effectively – an indispensable aspect of plant maintenance management as well as building maintenance scheduling, facility maintenance management and warehouse warehousing management.
SAP MM tutorial: Overview, Introduction to SAP MM
SAP MM allows you to process and examine invoices quickly and ensure timely payment for the goods and services provided.
Receivables management: SAP MM helps manage receivables so you can negotiate invoice amounts while receiving rapid payment for deliverables.
Account payables: Utilizing SAP MM module, invoices from purchasing department can be managed and discussed with vendors before being submitted for payment by accounts payable department.
Master data management: With SAP MM’s master data management feature, frequently-needed information can be stored into packages for easy sharing across departments.
By automating routine modifications of routine data, modification costs decrease drastically while saving valuable time in doing so.
SAP Material Management helps organizations address several aspects of materials and inventory management:
Buying Organization
Buying Methods
Material Value
Demand Planning
Stock Valuation
Stock Control
Material Needed
Locating Storage
Goods Delivery and
Verifying Invoices
What is SAP MM?
It allows organizations to control purchase requisition processes with this commercial procedure.
Companies now have the capability to streamline the supply chain process, ensuring costs and inventory levels remain at minimum and production runs efficiently.
While certain aspects are more essential than others, together they form one cohesive system that keeps operations flowing efficiently.
SAP FICO (Financial Accounting and Controlling) and SD (Sales and Distribution) modules often work alongside SAP MM to complete business functions.
SAP MM definition OR Define SAP MM
SAP Material and Inventory Management Module is used by businesses to manage material management and inventory control tasks within an organisation.
Companies benefit by making sure their inventory always contains sufficient supplies.
Furthermore, resource management becomes easier. They can more effectively oversee material flow from suppliers to warehouses and eventually clients; track material movements accurately; verify all transactions are accurate etc.
Organizations may use SAP MM to manage the purchase requisition process efficiently and control acquisition of supplies and goods more easily.
And while SAP MM defines itself, many organisations often struggle with how best to implement and use this module, for defining or explaining it is something else entirely!
What is Batch Management in SAP MM?
Batch management in SAP MM allows users to exercise control over the quantities or batches of materials being utilized during manufacturing processes, by keeping track of individual lots or batches that have been employed and creating records of them; as a result, product quality can be reliably guaranteed while expenses associated with each batch can also be monitored; all this ensures you make use of this powerful feature within SAP MM to make sense out of its potential shelf-life predictions!
What is Pricing Procedure In SAP MM?
SAP MM’s Pricing Process consists of rules used by the system to estimate the ultimate costs associated with goods or services purchased from vendors.
In particular, for purchase orders it outlines order, kind, computation of price components; tax calculations as well as levies such as surcharge, freight cost etc may also be taken into consideration in its calculations; tailoring this technique specifically to an organization can make its implementation seamless and more successful.
What is Master Data in SAP MM?
Master data in SAP MMM is utilized for internal as well as external procurement activities, with material quantities, descriptions, units of measure prices and cost calculations all stored within its Material Master record for inventory control purposes.
All this pertinent material information such as quantity descriptions unit measures costs calculations costsing information vendor details is kept safe for future reference within it’s Material Master Record to enhance operations governing buying/inventory control activities.
What is Scheduling Agreement in SAP MM?
A Scheduling Agreement (SA) in the SAP Materials Management (MM) module refers to an outline agreement between two parties whereby one party (usually, the vendor) promises that products or services they owe (typically customers) within an established time period, often contractual in nature and designed solely between vendors and customers (such as an agreement for purchasing certain kinds of product/service from certain vendors), known as Scheduling Agreements; including delivery dates, quantities required from clients (where applicable), attachment to orders as SAs and SAs can act as binding documents between parties (like any contract would).
What is Plant in SAP MM?
In SAP MM, Plant is defined as any combination of one or more Storage Locations with valid control parameters and master data which serves to manage inventory and material flow within an organization. Also referred to as plant-specific data.
What is Batch Record in SAP MM?
A “Batch Record” provides a detailed account of one batch of goods produced using specific materials and processes; its quality control testing; as well as any necessary rectification steps taken as soon as it was produced and released for sale or shipment.
When working within manufacturing environments, such data must be inputted into SAP systems in order to keep accurate tracking of materials and operations – for correct tracking as well as additional quality checks may need to be carried out later using it as reference material.
What is the pricing procedure in SAP MM?
SAP MM pricing processes are rules used by the system to compute the ultimate cost of goods or services purchased from vendors. A purchase order determines its own components – order type, kind, computation of prices components; calculation of taxes/levies as applicable and other levies related.
Furthermore, different price components – discounts rebates taxes surcharge freight material costs etc are all factored in to this pricing technique and it may even be tailored specifically to an organization’s individual needs.
What is Inventory Management in SAP MM?
Inventory Management in SAP MM refers to the practice of keeping an accurate record of available supplies, materials and completed items held by an organisation. It involves monitoring products throughout their supply chains – from production right up until their delivery to clients – in order to manage stock levels more effectively; identify when there is insufficient stock; plan production requirements more precisely and anticipate production needs more effectively. With this module you have all of the tools at your fingertips necessary for inventory monitoring: tracking flows of items as they pass from manufacture through distribution as well as keeping tabs on inventory levels!
What does SAP MM do and what is SAP MM used for?
What does SAP MM do?
SAP Material Management (MM) module offers end-to-end process integration for resource management, master data and material & resource planning.
SAP MM unifies and automates essential components of any company’s logistics and supply chain operations, from planning materials requirements and purchasing to receiving approval, analysing material value analysis, managing warehouse inventories as well as handling distribution.
As part of a complete logistics and supply chain management solution, this module delivers production planning, project administration, delivery tracking capabilities when combined with other modules.
What is SAP MM used for?
Customers utilizing this module use it to keep an inventory tracker, source materials from vendors at an economical cost and record goods flow. In particular, SAP MM is widely utilized as part of inventory control measures as well as cost oversights during material procurements and acquisition.
Master Data: Master data generation and upkeep include vendor master records, information about materials and vendors, price sources and quotations as well as material source details.
Material Valuation: Valuing materials involves both estimating their worth and allocating resources accordingly, such as charging purchasing organisations for purchase prices plus associated services like packing or delivery charges.
Goods Receipt & Movements: Receiving Materials and Verifying Storeroom. For goods movements, this may involve entry of delivery note data, invoice verification and posting for posting; while for reception it could include entry creation, allocation receipt posting as well as calculation of material amounts.
Invoice Verification: Invoice verification involves billing, finding, and procuring parts as well as keeping track of invoice quantities to maintain inventory or manage exceptions efficiently.
Application: This section details how to calculate material quantities using variable items, master formulas and key date clauses.
Quality Management: Quality management refers to the regulation of user and product standards. For instance, key dates or cycles dates could be created as well as product groups with associated dates for review purposes.
Confirmation: Confirmation sets the time frame and methodology for inspecting receipts and calculating quantities of materials received, with preferences set on confirmation message creation
Deviation Management: Deviation management refers to the detection, analysis, and resolution of deviations within your enterprise.
How does SAP MM work?
SAP Material Management (MM) is built upon data maintained in SAP, operating according to material requirement planning (MRP). MM’s goal is to supply production lines with necessary materials at just the right time in order to avoid delays due to resource scarcity issues.
As part of its goal to reduce stock gaps, Inventory Clear makes an effort to monitor inventory levels so businesses can meet sales deadlines effectively while decreasing lead times for replenishment and overall expenses.
Numerous strategies such as total cost of ownership and staff working on this module can help maintain material availability and usage within an organisation, as it performs numerous essential duties.
Important tasks may include inventory valuation, insert form valuation, conveyance, storage placement and volume transfer/verification as well as quantity verification.
As part of an effective operation within your organisation, this module enables you to effectively utilize material resources while taking expenses and shortages into consideration.
SAP Material Management offers purchasing requests, purchase orders, vendor masters, vendor evaluations, vendor code maintenance and integration as additional options for purchase requests and orders.
To effectively oversee materials, stocks and purchases for SAP ERP Central Component (ECC), SAP Material Management module must be present.
User can keep an eye on stock levels at warehouses. In addition, Inventory Pro comes equipped with various features designed to assist inventory managers throughout all steps.
SAP MM helps businesses keep an accurate accounting of their inventory by keeping an eye on stock locations and warehouse locations, while offering numerous features designed specifically to support inventory management processes across their life cycles.
What are the benefits of SAP MM?
Companies reap benefits from using this software’s efficient material management and procurement procedures as well as its many features for supporting inventory management throughout its complete lifecycle.
SAP MM assists businesses in effectively tracking purchases and stock levels to save both time and money when buying,
It boosts output by making sure resources never deplete, shortens purchasing times considerably and boosts output,
SAP MM ensures an efficient supply chain by simplifying purchasing and stocking operations.
It boosts productivity at work as expenses associated with buying and stock management are decreased, providing increased ROI over time.
SAP MM can save time and money by streamlining purchasing and stocking processes and guaranteeing uninterrupted supply chains.
It ensures timely deliveries of products while simultaneously saving on money by purchasing and tracking inventory more effectively – leading to improved efficiency and cost reductions. As a result, money savings become realized.
SAP Materials Management software helps manage material acquisition, inventories and supply chain shortages as well as vendor invoices and product verification, internal goods movements receipts as well as vendor receipts.
What Are The Advantages Of SAP MM?
Company Efficiency: SAP MM helps streamline transaction processing to increase company efficiency.
Cost Savings: SAP MM automates materials management from request to delivery for greater cost-cutting benefits by eliminating manual mistakes and improving accuracy.
Visibility: SAP MM provides unparalleled visibility into materials, inventories and the supply chain to enable seamless operations and ensure timely delivery of goods and services to clients.
Improved Cooperation: SAP MM optimizes department, supplier and customer collaboration so all parties involved share data efficiently and can work more closely together. This results in enhanced cooperation among parties involved and enhanced productivity overall.
What is SAP MM software and How to use SAP MM?
What is SAP MM software?
SAP Material Management software (MM) is part of SAP ERP which automates supply chains from raw material purchasing through distribution channels to client delivery, managing company inventory as well as vendor/item master data.
Plant Maintenance: The SAP Materials Management module handles maintenance orders, equipment upkeep and more.
How to use SAP MM or SAP MM Tutorial?
Enter Your SAP Login/Password.
Go To Logistics>Materials Management from SAP Easy Access (MM), AND (3) Select “Purchasing.”
Use the Purchasing panel to manage suppliers, purchase orders and requisitions.
Maintain stock levels using Inventory Management while producing goods receipts and monitoring purchase requisitions using Requisitioning Management.
Enter and pay bills using Invoice Verification for proper billing verification and entry.
The Commodities Movement module keeps tabs on stock and commodity movements, while Valuation and Account Assignment assists with costing inventory to account for it in your financial system.
Pay vendors via Account Payable.
Finally, the Reporting module gives you access to reports regarding all material management processes.
SAP MM Products
Material Master – SAP MM’s Material Master database provides organizations with information regarding all materials in use within them, including material descriptions, purchasing details and inventory levels.
Vendor Evaluation – Vendor evaluation allows organizations to ensure they work with only the top vendors available, which ensures optimal vendor partnerships are in place for business operations.
Purchasing – Purchasing is used to purchase materials and services from vendors, from creating purchase orders through tracking them to managing invoices to stock levels, reordering inventory levels and forecasting demand forecasting – this process involves creating purchase orders, tracking them to payment and managing invoices as part of an invoice management system
What is SAP MM Modules?
Procurement – This module facilitates vendor procurement. Inventory Control: The aim is to maintain adequate stock levels within your company.
Logistics Invoice Verification: Compare vendor invoices against procurement orders before being confirmed or denied as approved purchases.
Batch Management: Oversee manufacturing batches associated with operations.
Valuation & Account Assignment: Assign account numbers to goods purchased.
Material Requirements Planning (MRP): Schedule procurement operations.
Warehouse Management (WM): This module manages receiving, storing and shipping supplies.
Quality Management: This module ensures material and service quality. 9. Plant Maintenance: Manages preventative and corrective plant maintenance.
SAP MM Services
It oversees procurement and inventories.
It provides:
SAP material master data setup/administration
Inventory Control
Purchase from vendors
Valuing materials/ services.
Verifying Vendor Invoices against Purchase Orders.
Conduct-based Vendor Evaluation.
Physical Inventory: Stock Management
Vendor Consignments Arrangments
Inventory Optimization Reducing Expenses
Batch Management.
What are the best ways to learn SAP MM?
One option for learning SAP MM software usage step-by-step is taking an online SAP MM course, from reputed organizations like CloudFoundation. While taking one of several SAP MM classroom courses could also prove fruitful. When studying in this way, experts lead classes and provide answers for any inquiries raised during these lessons.
Read Literature: Books about SAP MM can provide invaluable guidance in learning this program, while online lessons cover its many complexities in-depth. When practising SAP MM create situations to aid learning – creating practise situations will speed your journey to mastery!
YouTube offers numerous SAP MM tutorials. SDN, Mentors and Tutorials provide training blogs and webpages specifically on SAP MM Training.
To further your SAP knowledge in SAP MM blogging start following expert blogs written by SAP professionals or specialists that offer tons of insight.
SAP MM lessons: These provide a broad system overview and foundation knowledge.
Online training videos: CloudFoundation & YouTube offers several SAP MM training videos which may quickly teach essentials of SAP MM.
Study Online: Online SAP MM courses may help expand your knowledge. Online classes could assist with understanding how this system operates.
Attend Training Workshops or Seminars: Gain expert guidance by joining one or more SAP MM workshops or seminars available both online and at physical locations.
SAP Materials Management (MM) provides inventory and material control. This module manages resources and inventory levels effectively – an indispensable aspect of plant maintenance management as well as building maintenance scheduling, facility maintenance management and warehouse warehousing management.
SAP MM tutorial: Overview, Introduction to SAP MM
SAP MM allows you to process and examine invoices quickly and ensure timely payment for the goods and services provided.
Receivables management: SAP MM helps manage receivables so you can negotiate invoice amounts while receiving rapid payment for deliverables.
Account payables: Utilizing SAP MM module, invoices from purchasing department can be managed and discussed with vendors before being submitted for payment by accounts payable department.
Master data management: With SAP MM’s master data management feature, frequently-needed information can be stored into packages for easy sharing across departments.
By automating routine modifications of routine data, modification costs decrease drastically while saving valuable time in doing so.
SAP Material Management helps organizations address several aspects of materials and inventory management:
Buying Organization
Buying Methods
Material Value
Demand Planning
Stock Valuation
Stock Control
Material Needed
Locating Storage
Goods Delivery and
Verifying Invoices
What is SAP MM?
It allows organizations to control purchase requisition processes with this commercial procedure.
Companies now have the capability to streamline the supply chain process, ensuring costs and inventory levels remain at minimum and production runs efficiently.
While certain aspects are more essential than others, together they form one cohesive system that keeps operations flowing efficiently.
SAP FICO (Financial Accounting and Controlling) and SD (Sales and Distribution) modules often work alongside SAP MM to complete business functions.
SAP MM definition OR Define SAP MM
SAP Material and Inventory Management Module is used by businesses to manage material management and inventory control tasks within an organisation.
Companies benefit by making sure their inventory always contains sufficient supplies.
Furthermore, resource management becomes easier. They can more effectively oversee material flow from suppliers to warehouses and eventually clients; track material movements accurately; verify all transactions are accurate etc.
Organizations may use SAP MM to manage the purchase requisition process efficiently and control acquisition of supplies and goods more easily.
And while SAP MM defines itself, many organisations often struggle with how best to implement and use this module, for defining or explaining it is something else entirely!
What is Batch Management in SAP MM?
Batch management in SAP MM allows users to exercise control over the quantities or batches of materials being utilized during manufacturing processes, by keeping track of individual lots or batches that have been employed and creating records of them; as a result, product quality can be reliably guaranteed while expenses associated with each batch can also be monitored; all this ensures you make use of this powerful feature within SAP MM to make sense out of its potential shelf-life predictions!
What is Pricing Procedure In SAP MM?
SAP MM’s Pricing Process consists of rules used by the system to estimate the ultimate costs associated with goods or services purchased from vendors.
In particular, for purchase orders it outlines order, kind, computation of price components; tax calculations as well as levies such as surcharge, freight cost etc may also be taken into consideration in its calculations; tailoring this technique specifically to an organization can make its implementation seamless and more successful.
What is Master Data in SAP MM?
Master data in SAP MMM is utilized for internal as well as external procurement activities, with material quantities, descriptions, units of measure prices and cost calculations all stored within its Material Master record for inventory control purposes.
All this pertinent material information such as quantity descriptions unit measures costs calculations costsing information vendor details is kept safe for future reference within it’s Material Master Record to enhance operations governing buying/inventory control activities.
What is Scheduling Agreement in SAP MM?
A Scheduling Agreement (SA) in the SAP Materials Management (MM) module refers to an outline agreement between two parties whereby one party (usually, the vendor) promises that products or services they owe (typically customers) within an established time period, often contractual in nature and designed solely between vendors and customers (such as an agreement for purchasing certain kinds of product/service from certain vendors), known as Scheduling Agreements; including delivery dates, quantities required from clients (where applicable), attachment to orders as SAs and SAs can act as binding documents between parties (like any contract would).
What is Plant in SAP MM?
In SAP MM, Plant is defined as any combination of one or more Storage Locations with valid control parameters and master data which serves to manage inventory and material flow within an organization. Also referred to as plant-specific data.
What is Batch Record in SAP MM?
A “Batch Record” provides a detailed account of one batch of goods produced using specific materials and processes; its quality control testing; as well as any necessary rectification steps taken as soon as it was produced and released for sale or shipment.
When working within manufacturing environments, such data must be inputted into SAP systems in order to keep accurate tracking of materials and operations – for correct tracking as well as additional quality checks may need to be carried out later using it as reference material.
What is the pricing procedure in SAP MM?
SAP MM pricing processes are rules used by the system to compute the ultimate cost of goods or services purchased from vendors. A purchase order determines its own components – order type, kind, computation of prices components; calculation of taxes/levies as applicable and other levies related.
Furthermore, different price components – discounts rebates taxes surcharge freight material costs etc are all factored in to this pricing technique and it may even be tailored specifically to an organization’s individual needs.
What is Inventory Management in SAP MM?
Inventory Management in SAP MM refers to the practice of keeping an accurate record of available supplies, materials and completed items held by an organisation. It involves monitoring products throughout their supply chains – from production right up until their delivery to clients – in order to manage stock levels more effectively; identify when there is insufficient stock; plan production requirements more precisely and anticipate production needs more effectively. With this module you have all of the tools at your fingertips necessary for inventory monitoring: tracking flows of items as they pass from manufacture through distribution as well as keeping tabs on inventory levels!
What does SAP MM do and what is SAP MM used for?
What does SAP MM do?
SAP Material Management (MM) module offers end-to-end process integration for resource management, master data and material & resource planning.
SAP MM unifies and automates essential components of any company’s logistics and supply chain operations, from planning materials requirements and purchasing to receiving approval, analysing material value analysis, managing warehouse inventories as well as handling distribution.
As part of a complete logistics and supply chain management solution, this module delivers production planning, project administration, delivery tracking capabilities when combined with other modules.
What is SAP MM used for?
Customers utilizing this module use it to keep an inventory tracker, source materials from vendors at an economical cost and record goods flow. In particular, SAP MM is widely utilized as part of inventory control measures as well as cost oversights during material procurements and acquisition.
Master Data: Master data generation and upkeep include vendor master records, information about materials and vendors, price sources and quotations as well as material source details.
Material Valuation: Valuing materials involves both estimating their worth and allocating resources accordingly, such as charging purchasing organisations for purchase prices plus associated services like packing or delivery charges.
Goods Receipt & Movements: Receiving Materials and Verifying Storeroom. For goods movements, this may involve entry of delivery note data, invoice verification and posting for posting; while for reception it could include entry creation, allocation receipt posting as well as calculation of material amounts.
Invoice Verification: Invoice verification involves billing, finding, and procuring parts as well as keeping track of invoice quantities to maintain inventory or manage exceptions efficiently.
Application: This section details how to calculate material quantities using variable items, master formulas and key date clauses.
Quality Management: Quality management refers to the regulation of user and product standards. For instance, key dates or cycles dates could be created as well as product groups with associated dates for review purposes.
Confirmation: Confirmation sets the time frame and methodology for inspecting receipts and calculating quantities of materials received, with preferences set on confirmation message creation
Deviation Management: Deviation management refers to the detection, analysis, and resolution of deviations within your enterprise.
How does SAP MM work?
SAP Material Management (MM) is built upon data maintained in SAP, operating according to material requirement planning (MRP). MM’s goal is to supply production lines with necessary materials at just the right time in order to avoid delays due to resource scarcity issues.
As part of its goal to reduce stock gaps, Inventory Clear makes an effort to monitor inventory levels so businesses can meet sales deadlines effectively while decreasing lead times for replenishment and overall expenses.
Numerous strategies such as total cost of ownership and staff working on this module can help maintain material availability and usage within an organisation, as it performs numerous essential duties.
Important tasks may include inventory valuation, insert form valuation, conveyance, storage placement and volume transfer/verification as well as quantity verification.
As part of an effective operation within your organisation, this module enables you to effectively utilize material resources while taking expenses and shortages into consideration.
SAP Material Management offers purchasing requests, purchase orders, vendor masters, vendor evaluations, vendor code maintenance and integration as additional options for purchase requests and orders.
To effectively oversee materials, stocks and purchases for SAP ERP Central Component (ECC), SAP Material Management module must be present.
User can keep an eye on stock levels at warehouses. In addition, Inventory Pro comes equipped with various features designed to assist inventory managers throughout all steps.
SAP MM helps businesses keep an accurate accounting of their inventory by keeping an eye on stock locations and warehouse locations, while offering numerous features designed specifically to support inventory management processes across their life cycles.
What are the benefits of SAP MM?
Companies reap benefits from using this software’s efficient material management and procurement procedures as well as its many features for supporting inventory management throughout its complete lifecycle.
SAP MM assists businesses in effectively tracking purchases and stock levels to save both time and money when buying,
It boosts output by making sure resources never deplete, shortens purchasing times considerably and boosts output,
SAP MM ensures an efficient supply chain by simplifying purchasing and stocking operations.
It boosts productivity at work as expenses associated with buying and stock management are decreased, providing increased ROI over time.
SAP MM can save time and money by streamlining purchasing and stocking processes and guaranteeing uninterrupted supply chains.
It ensures timely deliveries of products while simultaneously saving on money by purchasing and tracking inventory more effectively – leading to improved efficiency and cost reductions. As a result, money savings become realized.
SAP Materials Management software helps manage material acquisition, inventories and supply chain shortages as well as vendor invoices and product verification, internal goods movements receipts as well as vendor receipts.
What Are The Advantages Of SAP MM?
Company Efficiency: SAP MM helps streamline transaction processing to increase company efficiency.
Cost Savings: SAP MM automates materials management from request to delivery for greater cost-cutting benefits by eliminating manual mistakes and improving accuracy.
Visibility: SAP MM provides unparalleled visibility into materials, inventories and the supply chain to enable seamless operations and ensure timely delivery of goods and services to clients.
Improved Cooperation: SAP MM optimizes department, supplier and customer collaboration so all parties involved share data efficiently and can work more closely together. This results in enhanced cooperation among parties involved and enhanced productivity overall.
What is SAP MM software and How to use SAP MM?
What is SAP MM software?
SAP Material Management software (MM) is part of SAP ERP which automates supply chains from raw material purchasing through distribution channels to client delivery, managing company inventory as well as vendor/item master data.
Plant Maintenance: The SAP Materials Management module handles maintenance orders, equipment upkeep and more.
How to use SAP MM or SAP MM Tutorial?
Enter Your SAP Login/Password.
Go To Logistics>Materials Management from SAP Easy Access (MM), AND (3) Select “Purchasing.”
Use the Purchasing panel to manage suppliers, purchase orders and requisitions.
Maintain stock levels using Inventory Management while producing goods receipts and monitoring purchase requisitions using Requisitioning Management.
Enter and pay bills using Invoice Verification for proper billing verification and entry.
The Commodities Movement module keeps tabs on stock and commodity movements, while Valuation and Account Assignment assists with costing inventory to account for it in your financial system.
Pay vendors via Account Payable.
Finally, the Reporting module gives you access to reports regarding all material management processes.
SAP MM Products
Material Master – SAP MM’s Material Master database provides organizations with information regarding all materials in use within them, including material descriptions, purchasing details and inventory levels.
Vendor Evaluation – Vendor evaluation allows organizations to ensure they work with only the top vendors available, which ensures optimal vendor partnerships are in place for business operations.
Purchasing – Purchasing is used to purchase materials and services from vendors, from creating purchase orders through tracking them to managing invoices to stock levels, reordering inventory levels and forecasting demand forecasting – this process involves creating purchase orders, tracking them to payment and managing invoices as part of an invoice management system
What is SAP MM Modules?
Procurement – This module facilitates vendor procurement. Inventory Control: The aim is to maintain adequate stock levels within your company.
Logistics Invoice Verification: Compare vendor invoices against procurement orders before being confirmed or denied as approved purchases.
Batch Management: Oversee manufacturing batches associated with operations.
Valuation & Account Assignment: Assign account numbers to goods purchased.
Material Requirements Planning (MRP): Schedule procurement operations.
Warehouse Management (WM): This module manages receiving, storing and shipping supplies.
Quality Management: This module ensures material and service quality. 9. Plant Maintenance: Manages preventative and corrective plant maintenance.
SAP MM Services
It oversees procurement and inventories.
It provides:
SAP material master data setup/administration
Inventory Control
Purchase from vendors
Valuing materials/ services.
Verifying Vendor Invoices against Purchase Orders.
Conduct-based Vendor Evaluation.
Physical Inventory: Stock Management
Vendor Consignments Arrangments
Inventory Optimization Reducing Expenses
Batch Management.
What are the best ways to learn SAP MM?
One option for learning SAP MM software usage step-by-step is taking an online SAP MM course, from reputed organizations like CloudFoundation. While taking one of several SAP MM classroom courses could also prove fruitful. When studying in this way, experts lead classes and provide answers for any inquiries raised during these lessons.
Read Literature: Books about SAP MM can provide invaluable guidance in learning this program, while online lessons cover its many complexities in-depth. When practising SAP MM create situations to aid learning – creating practise situations will speed your journey to mastery!
YouTube offers numerous SAP MM tutorials. SDN, Mentors and Tutorials provide training blogs and webpages specifically on SAP MM Training.
To further your SAP knowledge in SAP MM blogging start following expert blogs written by SAP professionals or specialists that offer tons of insight.
SAP MM lessons: These provide a broad system overview and foundation knowledge.
Online training videos: CloudFoundation & YouTube offers several SAP MM training videos which may quickly teach essentials of SAP MM.
Study Online: Online SAP MM courses may help expand your knowledge. Online classes could assist with understanding how this system operates.
Attend Training Workshops or Seminars: Gain expert guidance by joining one or more SAP MM workshops or seminars available both online and at physical locations.
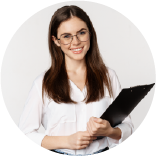
Sindhuja
Author