Six Sigma Interview Questions and Answers
Six Sigma technology can transform our approach to quality management and process enhancement; its data-driven methodology aims to minimise defects while increasing efficiency.
1. What is Six Sigma?
Six Sigma’s management strategy centres around eliminating process defects and supporting change through sustainable measures.
As part of an organisation’s DMACC problem-solving method, Six Sigma projects directly contribute to increasing their bottom line.
2. What is DMAIC and DMADV?
DMAIC is used in Six Sigma to optimise existing processes by identifying issues and opportunities for improvements and meeting customer requirements.
3. What is the purpose of implementing Six Sigma in various industries?
Implementing Six Sigma can enable companies to boost production, strengthen customer relations, and increase productivity.
4. What is Lean methodology?
Lean methodology emphasises providing value to customers by eliminating waste and decreasing cycle times.
5. What is the difference between Lean and Six Sigma?
Lean emphasises eliminating waste and shortening cycle times, while Six Sigma refers to an overall management approach that supports DMACC problem-solving methods using statistical methodologies for problem analysis.
6. What are the benefits of Lean Six Sigma for businesses?
Lean Six Sigma can bring numerous advantages to any organisation, including increased profits, simplified and standardised processes, reduced errors, employee development opportunities and customer value creation.
7. What is Quality?
Quality can be defined as the level of excellence provided to customers for products or services offered, with customer satisfaction serving as its ultimate aim for improved quality.
8. What is a business system?
A business system is intended to implement processes, ensure inputs are in their appropriate places at the correct times, collect and analyse data for continuous improvement, and collect feedback to drive further process innovation.
9. What levels does SIX Sigma cover?
SIX Sigma features five levels: negatives, champions, black belts and green belts; each level outlines negative aspects within an organisation while outlining vision and mission statements in successive steps.
10. What is the balanced scorecard (BSC)?
A balanced scorecard (BSC) provides a holistic framework for strategy implementation and performance measurement that considers perspectives beyond financial ones.
11. How does the BSC framework work?
To put into action, the BSC framework involves setting strategic objectives, measures, targets and initiatives for each perspective while ensuring high-level metrics link with lower-level operations measures.
12. What are the constraints in Lean?
Lean constraints involve identifying issues within processes to help organisations effectively implement lean principles.
13. What is the Pareto Chart?
A Pareto Chart, also called an 80-20 rule or vital few trivial many charts, helps project teams focus on issues causing most defects or complaints,emphasising how 80% of their effects stem from 20% of causes.
14. What is the Network diagram?
Network diagrams are often employed by Project Managers when planning projects, typically starting and ending with one single event on both ends; there should not be multiple beginning and ending points on such diagrams.
15. How is the balanced scorecard developed?
A balanced scorecard requires considering each perspective’s strategic objectives, measures, targets, and initiatives. It includes high-level metrics linked to lower-level operational measures with target values set for every measure outlined on it.
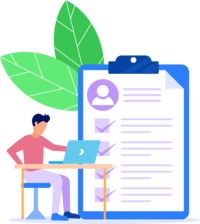
Six Sigma Training
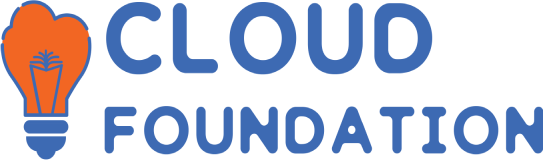
Quality Function Deployment is a data-driven methodology that uses key performance indicators (KPIs) in business processes to help identify any constraints in performance and then implement decisions to enhance overall business operations and increase performance.
17. What is the FMEA Risk Priority Number?
Ideally, companies use FMEA Risk Priority Number to help understand customer requirements more fully and develop competitive products more rapidly at reduced costs.
18. What is benchmarking in DMACC?
Benchmarking is an aspect of DMACC that compares an organisation’s business processes, practices and performance measures with those of industry leaders; there are various forms of benchmarking, such as process benchmarking, financial benchmarking, performance benchmarking, product benchmarking, strategic functional competitive and collaborative benchmarking.
19. What is Stakeholder analysis?
Stakeholder analysis is essential when undertaking any Six Sigma project, as it involves identifying and assessing any impact on stakeholders such as customers, suppliers, company management, employees or society who could oppose change efforts.
20. What is Process ownership?
Process ownership is when an individual or team assumes full accountability for overseeing and carrying out a specific business process within an organisational hierarchy and ensures it runs seamlessly while satisfying customers’ requirements.
21. What are internal customers?
Internal customers refer to employees or staff members whose decisions directly influence final customers, system processes and product or service quality in some way.
22. What are external customers?
External customers refer to end-users of products and exterior services,which serve as agents for process improvement projects by driving higher perceived quality and productivity levels in products or external services.
23. What is QFD?
QFD is an established methodology for understanding and translating customer requirements into product designs at lower costs; it helps organisations focus on customers while creating more innovative, competitive offerings at reduced costs.
24. What is a check sheet?
Production processes often use structured forms for collecting and analysing data in production environments, typically when collecting can be repeated by one individual or location over multiple instances.
25. How can ANOVA be performed in MINITAB?
MINITAB offers the capability of performing ANOVA by stacking data in two columns and selecting delivery time as response and factor as outlet as variables for analysis.
26.What is the 5Y technique in statistics?
The 5Y technique is a statistical technique designed to analyse the root cause of problems by highlighting specific elements within an issue that make up its core.
27. What is a 6-sigma green belt?
A Six Sigma green belt is a team member who assists with process improvement, projects, data gathering, and problem-solving initiatives, and theyhelp their project leader gather and analyse data sets as part of process analyses conducted and propose improvements and solutions.
28. What is the Affinity Diagram Method in problem-solving?
The Affinity Diagram Method is an approach individuals or teams use to group ideas and identify common themes; anorganisation with dissatisfied employees could represent itself through sticky notes arranged according to categories or thought patterns on an Affinity Diagram, which helps group thoughts with similar themes.
29. What is the central limit theorem (CLT)?
Central Limit Theorem states that for sample sizes greater than 30, sample means are generally very close to population means; that means the standard error of Mean, representing variability amongst sample means and less than the population standard deviation value, is generally below 30% of SD value of population standard deviation.
30. What is the difference between range, variance, and standard deviation?
A range is the difference between data’s most significant and least significant values; variance refers to differences between maximum and minimum values; standard deviation provides the ultimate measure of dispersion relative to the mean.
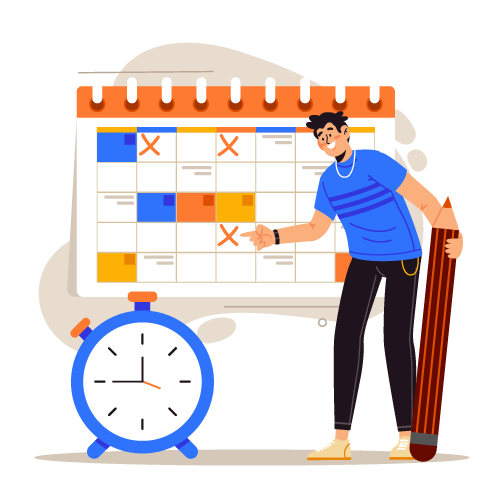
Six Sigma Online Training
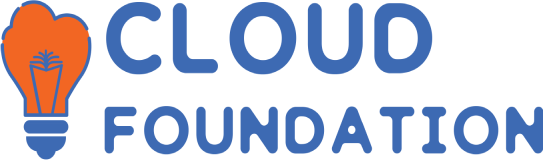
31. What is the F-test, and how is it used?
An F-test is a statistical test used to compare variances of two data groups to ascertain a statistically significant disparity in their variances.
32. What is the paired t-test, and how is it used?
A paired t-test is a statistical test used to compare the effectiveness of improvement measures, specifically training programs; itmeasures whether there has been a statistically significant change before and after engaging in training activities.
33. What is the sample variance, and how is it calculated?
Sample variance refers to the average of all squared differences from the mean; its calculation involves subtracting each data point’s mean from its respective data points before squaring its result and then averaging over all squares produced.
34. What is ANOVA, and how is it used?
ANOVA is a statistical test that compares variances of more than two groups to determine if any sample means are unequal – this allows further testing on these issues.
35. What is MINITAB, and what can it be used for?
MINITAB is an advanced statistical software package that can be used for various statistical tests, including ANOVA and hypothesis testing.
36. What is the chi-square distribution, and how is it used?
The chi-square distribution is an often-utilized hypothesis testing technique for calculating the probability that the sum of squares k independent standard normal random variables co-occurs.
37. What is the Friedman test, and how is it used?
The Friedman test is a nonparametric statistical technique designed to compare median values across samples from separate populations to ascertain whether significant statistical differentiation exists among them.
38. What is the Critical Path Method (CPM)?
Project Managers use the Critical Path Method as an indispensable tool in monitoring project progress and ensuring it stays on schedule; a critical path consists of the most extended sequence of tasks on any network diagram with zero slack for all functions; its identification ensures smooth project execution while minimising rework costs.
To find out how much you’ve learned, do these multiple-choice exams.
39. What is the first step of DMADV methodology?
Defining customer requirements.
Creating a specification.
Analysing the product to identify areas of improvement.
Replacing faulty machines.
40. What is the final step of DMADV methodology?
Defining issues.
Replacing faulty machines.
Testing the product and making improvements.
Analysing the product to identify areas of improvement.
41. Which of the following is not a key benefit of implementing Six Sigma?
Improved customer loyalty
Increased production
Higher productivity
Reduced cycle time
42. Which of the following is NOT a benefit of Lean Six Sigma?
Increased profits
Standardised and simplified processes
Reduced errors
Improved customer satisfaction
43. What is the systematic approach to improving an organisation’s performance that Six Sigma follows?
Five levels of improvement: negatives, champions, black belts, and green belts
Four parts of a process: input, process steps, output, and feedback
DMACC method of problem-solving
Six Sigma Level chart
Conclusion
Six Sigma technology boosts business efficiency and process improvement, data analysis and statistics are used to find and fix errors, minimize variability, and improve quality, with its focus on continuous improvement and customer satisfaction, Six Sigma is crucial to many firms worldwide.
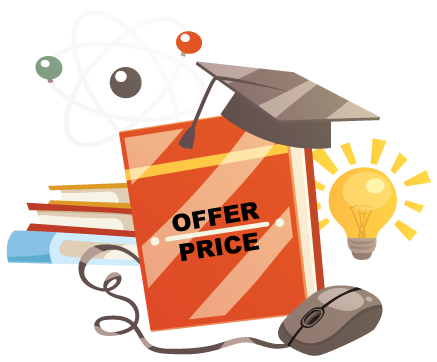
Six Sigma Course Price
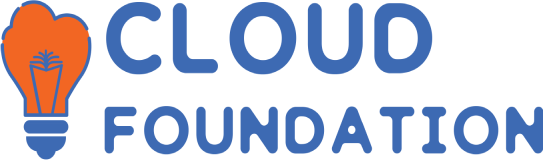
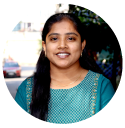
Srujana
Author