SAP PP Interview Questions
SAP PP Interview Questions!!! Are you prepared for the SAP PP (Production Planning) interview questions and answers?
Look no further –lets learn interview questions for SAP PP (Production Planning)which provides tremendous solutions to streamline procedures while sharpening organizational skills – but first, you must master the interview!
Are you nervous before interviews? Rest assured, our comprehensive guide crafted by experienced authors will equip you with all the necessary tools to fearlessly address any challenge and achieve all your goals! Our guide is here, so get ready!
So, create an excellent first impression and ready to ace that interview!
SAP PP Interview Questions and Answers:
1. What is SAP PP and why is it a popular choice for clients?
SAP PP is a leading Enterprise Resource Planning (ERP) product or package. Its popularity lies in its functionality and integration with various organizational models.
2. What does materials management involve in SAP PP?
Materials management deals with the procurement activities of an organization, including identifying material needs, interactions with suppliers, creating orders, checking material quality, placing in the warehouse, and releasing payment to vendors.
3. What is the role of production planning in SAP PP?
Production planning involves various types of plans, such as make to order planning and make to stock planning.
4. What does quality management ensure in SAP PP?
Quality management ensures that all materials meet business requirements, whether they are inward or outward.
5. What is the role of planning maintenance in SAP PP?
Planning maintenance involves regular services and maintenance activities for machinery and equipment used in manufacturing units, factories, or sites.
6. What is the function of financial accounting and controlling in SAP PP?
Financial accounting and controlling covers payments from customers and suppliers.
7. What is the role of service management in SAP PP?
Service management includes customer and admin departments, such as human resources.
8. What are the two types of procurement and how does SAPPP handle them?
Procurement types are classified into external and internal procurement.
External procurement involves a customer or company supplying a finished material, while internal procurement involves a demand management or independent requirement plan.
SAP uses a material requirement plan (MRP) to handle these processes.
9. What is MRP and how does it work in SAP PP?
Business process MRP assures stock availability for manufacturing. Inventory management and bill of material data are included. If the corporation doesn’t have enough stock to fulfil a client order, it will plan and construct one.
A sub-purchase order will be placed if the firm possesses the incorrect material. The manager, senior manager, or vice president, depending on organization structure, will approve this order.
10. What is the total procurement process and which models does it fall under?
The total procurement process includes identifying the need for the material up to payment to the vendor. This process falls under the procurement call, external procurement, and materials management models.
11. What is the difference between external and internal procurement in terms of time and process flow?
External procurement takes less time and involves procuring materials from outside the organization through a production order.
Internal procurement, on the other hand, takes more time as the material is already within the organization and is added to the department.
12. What role do functional consultants play in the implementation of the SAP ERP system?
A group of functional consultants is involved in designing and framing the organization structure in the SAP ERP system. They are responsible for understanding the client’s business process and defining the organization structure.
13. What is the SAP PP consultant’s role in the SAP ERP system?
The SAP PP consultant gathers information from other consultants to create organization parameters in the SAP ERP system. They do not create any organizations themselves.
14. What is the starting point of the business process in SAP ERP?
The business process in SAP ERP starts with the Material Requirement Planning (MRP), plant order, cut one 2, and action procurement.
15. What is master data in the SAP ERP system and how is it used?
Master data is a concept in SAP ERP that is created in each functional module during the implementation phase. These master data are available in the SAPR software and are used throughout the company’s life.
One-time activities cannot be recorded, so it is necessary to frame all master data at the beginning of the PPT.
16. First steps in SAP Shuffle configuration for a new production planning module?
creating order types that determine the production order or process order configuration in the plant.
17. Order-type-dependent parameters for status profiles and routing may be found where?
These parameters can be accessed through SPRO (SAP Project Reference Object) or directly using transaction OPL8.
18. Standard and reverb order kinds allocate number ranges using what number series?
Standard production order types use the seven series and reverb order types use the nine series.
19. How does the production schedule profile default protection or reverb order kinds for various scenarios?
It helps default protection or reverb order types based on scenarios like make to stock, make to order, or rework.
20. What is the purpose of the production supervisors’ unique codes in OPJ 9?
These codes can be configured in OPJ 9 by assigning a three-digit code to them and are defaulted into the production orders when creating a production order.
21. Users may manage missing component checks during production order formation in which transaction?
The checking control for missing parts during the creation of production orders can be controlled in OPJ K.
22. Where can scheduling parameters for production orders be used?
These parameters can be used in OPU3, which automatically copies the parameters into the production orders when created.
23. Rework activities may use default settings for operation generation in which transaction?
Default values for the generation of operations for rework activities can be done directly in OPJG transactions.
24. What is the use of the production node in SPRO for the discrete manufacturing process?
The production node in SPRO (SAP Project Reference Object) is used for the discrete manufacturing process and includes basic data, activities, sub-notes, bill of material work centers, routing, and execution steps.
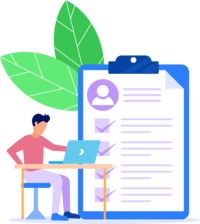
SAP PP Training
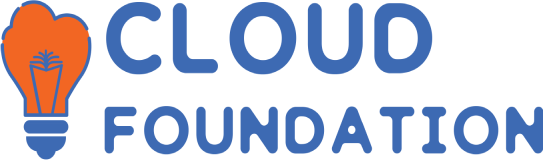
25. Short-floor settings for off-floor control are where in the SPRO production node setup?
The short-floor parameters related to off-floor control have a sub-node in the production node setup.
26. SAP production order type configuration begins with what steps, and what nodes discuss order types?
The initial steps include discussing order types such as standard production orders (pp01) and process orders (01) in the first node.
27. Production order status management—why and how are status profiles created?
Status management helps define user status for each order type, and status profiles can be created in BS02 or BS01.
28. Which parameters are specified by plant and order type after manufacturing order type completion?
Order type dependent parameters including the production version, routing-related data, and number increment for operations are configured based on the plant and order type combination.
29. What application is used for production orders that require batch determination during creation or release?
The BOM application is used for production orders that require batch determination during creation or release.
30. How many purchase acquisitions should be created during the release process for a production order?
Half the purchase acquisitions should be created during the release process to control the creation of the purchase regulation for the operation outsourcing.
31. What can be tracked using change documents for the order header and material operation in a production order?
Change documents track status changes related to the order’s creation, release, and confirmation.
32. What documentation can be activated to track goods movement under production orders?
Documentation of goods movement under production orders can be activated to track goods receipt in the order itself.
33. In the casting department, what key can be assigned to order time-dependent parameters?
The casting department can assign planned variance, actual variance, and resultant analysis key to order time-dependent parameters.
34. What are the functions of the two check boxes for creation and release in SAP production orders?
One check box is for printing production order or shop papers upon releasing the order, another for rerunning the scheduling part on the order, and one for instant release at the time of creation.
35. What are metal availability checks used for in production orders?
Metal availability checks confirm partial available quantities on components.
36. What can be done automatically when a confirmation is posted in a production order?
Finished products can be automatically placed into the finished storage location or quarantine location.
37. What is the role of batch management in production orders?
Batch management allows for automatic batch creation at the time of creation or release, and batch classification is important for execution in the foreground or background.
38. What are the options for managing collective conversion in production orders?
Users can choose options for creating or releasing production orders, saving or not creating the order, and deciding whether to create or save the order.
39. What are the functions of production scheduling profiles in SAP production orders?
Production scheduling profiles can be configured based on scenarios like make to stock, make to order production, and project management systems.
40. What is the role of the production supervisor code in SAP production orders?
The production supervisor code can create the alpha and enable availability checks for material availability, component availability, and capacity availability.
41. What are the scheduling parameters in SAP production orders, and what are their functions?
Scheduling parameters define the scheduling type that the production order should have as default, with forward scheduling for production orders and backwards scheduling for copied orders. The star option allows any order created in a specific plant to have all parameters as default.
42. What configurations are available in SAP related to reductions of operations and bottlenecks?
Configurations related to reductions of operations and bottlenecks are also available in SAP.
43. In which industries is SAP Production Planning and Execution (PPE) used, and what are its functions?
SAP Production Planning and Execution (PPE) is used in various industries, including bike manufacturing, car manufacturing, engine assembly, and pharmaceutical manufacturing.
It is used to plan production processes, including the assembly of specific parts, flow, time, and material requirements, and is part of the logistic area where it supports production planning and master data management.
44. What level of commitment is required to learn SAP PPE?
Learning SAP PPE is not restricted to specific industries but requires a desire and commitment. Knowledge is required for various manufacturing business processes, but it is not mandatory.
45. What is the role of SAP PPE in SAP, and why is its knowledge essential?
SAP PPE is a crucial module in SAP, and its knowledge should be applied to day-to-day scenarios in industries. It is essential to learn from both a configuration and user-level perspective, as well as from an end-user perspective. From this blog you can also learn SAP PP module interview questions.
46. How is a BOM used in SAP PP for production planning, and what is the one-to-one ratio?
In SAP PP, a BOM is used for production planning by entering a quantity for a product and the system calculates the necessary components.
The base quantity is set at one, and the system uses a one-to-one ratio to calculate the quantity needed for each item, ensuring accurate and efficient production planning.
47. What is a BOMer number, and how is it generated in SAP PP?
For each BOM created, the system generates a BOMer number, which can be changed or saved. This number can be used by other departments like production, salespeople, plant maintenance, and costing.
48. What are the benefits of using a BOM in SAP PP for various purposes, such as production, salespeople, plant maintenance, and costing?
The system uses a one-to-one ratio to calculate the required components for each item, ensuring accurate and efficient production planning.
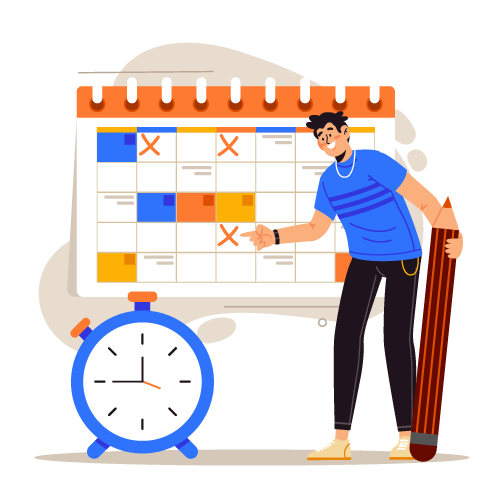
SAP PP Training
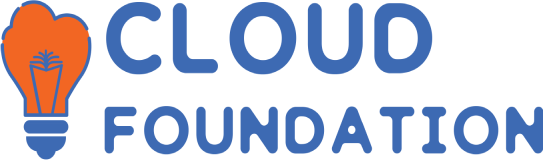
49. How can a BOM be created for a document in SAP PP, and what are the different BOM statuses?
In the CV11 document, users can create a BOM for a document, which is a drawing similar to a final assembly drawing. The default BOM status is 01, which means that the BOM can be used in MRP, planned order, and other parts of the business.
Different statuses can be selected to limit the use of the BOM to specific departments or parts of the business.
50. What is the role of BOM status and header level in Excel for restricting specific functions in SAP PP?
The BOM status and header level in Excel allow for specific functions to be restricted. There are seven BOM statuses available, each with its own purpose, and customizing your own status is possible through the SPRO (SAP Project Reference Object) section.
51. At the item level, what functions can be specified for engineering, production, plant, spare parts, sales, or costing?
At the item level, you can specify which items to use for engineering, production, plant, spare parts, sales, or costing.
For example, you can select one item and click on the icon to view its detail, and you can also specify costing relevance at the item level only.
52. What is low level coding in SAP PP, and how is it related to BOMs?
Low level coding in SAP PP refers to a BOM having multiple BOMs, each with its own BOM. For example, a pump made of a casing, flywheel, and shaft has two components, each with its own BOM. This is known as low level coding.
53. What is a group BOM in SAP PP, and how can it be created?
A group BOM is created without entering a plant, but rather a single BOM created for a common BOM for every plant. To create a group BOM, the plant should be empty and press enter.
The user can ignore the warning that indicates a group BOM is being created by pressing enter again.
54. Why does the BOM number remain the same when assigning two plants, and what is the role of the notary system?
The BOM number remains the same when assigning two plants due to the notaryd system, which ensures consistency across plants.
55. How are group BOMs created and assigned in a plant management system, and what is their impact on plant assignments?
Group BOMs are created without entering a plant, and when they are assigned to different plants, the group BOM number remains the same for the assigned plant.
However, if a component is created independently from another plant, it will not be affected by any changes made at the group BOM level.
56. What is the difference between creating a BOM independently and copying from a group BOM in terms of plant assignments?
Creating a separate one-plant BOM for each plant will result in different BOM numbers, while copying from a group BOM will result in the same BOM number for that specific plant.
Changes made at the group BOM level will affect the plant level, while changes made at the individual plant level will not affect the copied BOM.
57. What is a BOM structure, and what are its components?
A BOM structure consists of headers, items, and sub-items. Each item has its own features, unit of measure, quantity, and setup.
Sub-items can also be assigned to an item number for more customization, but they have no control function and have limited options or features.
58. What are the different item categories that users can select when creating a BOM in SAP PP?
Users can select different categories such as stock item, non-stroke item, variable size item, item text, document item, class item, and PM structure element when creating a BOM.
59. What is the process for creating a drawing document and assigning it to a BOM in SAP PP?
Users can upload and assign drawing documents to a BOM, or they can create their own drawings using the translation tool CV01 and attach files to a BOM.
60. What is the concept of recursion in manufacturing, and how can it be used in various industries?
Recursion is a concept in manufacturing where the same product is produced at different levels of the production process. It can be used in various industries, such as manufacturing a laptop or a pump, and in chemical industries.
To enable recursion, users must check the box for recursion in the item level. Additionally, co-products allow for the production of a finished product from a raw material.
61. What are the various aspects of inventory management, and what do they entail?
several aspects of inventory management in a production management system. the concept of minus quantity, which means that certain items will be added to the stock, while others will be consumed.
Alternativeitem groups, which are used for the same product but with different properties or vendors. Explosiontype, which is a type of explosion where a phantom assembly is used. fix quantity, which means an item will not be used proportionally in the production process.
62. What is inventory management in a production management system?
The various aspects of inventory management in a production management system, including item status and production costing, material provision and spare parts, deletion of BOMs and BOM reporting.
63. What is the role of the item status and production costing section in inventory management, and how can it be adjusted?
The item status and production costing section allow users to adjust the item’s relevance for costing based on its importance.
64. How can users delete items in a BOM, and what are the different types of BOM reporting available?
Users can delete items in a BOM by selecting the item and clicking on the delete button, saving it, and entering new items. BOM reporting is available in three types: CS11-turnation, CS12, and CS13, with different features such as showing the reporting BOM level by level, multi-level structure BOM, and summarized BOM.
65. What are the benefits of using BOM reporting in a production management system, and how are BOM components displayed in the report?
BOM reporting provides users with a better understanding and management of the system by displaying the total number of items in a BOM, with each item having its own BOM.
BOM components are displayed in the report with their own BOMs, such as ABC1 and ABC12.3, and the level of BOM is displayed on the left side of the report.
66. What are the functions that users can perform in the BOM report, and how does it allow for better management of the system?
Users can save, execute, and delete sub items in the BOM report, providing them with better understanding and management of the system.
67. What is the purpose of a BOM in inventory management, and how is the total quantity of the BOM displayed?
A BOM is used to show the total quantity of the BOM, which includes the total quantity from all levels. This is called BOM explosion or reporting within a BOM.
68. What does the system provide in terms of analysing and reporting on the total number of items in a BOM?
The system provides a comprehensive view of the total number of items in a BOM, allowing for detailed analysis and reporting.
69. What transaction is not commonly used but helps identify common materials and their impact on the business?
The transaction CS14 is not commonly used but it helps identify common materials and their impact on the business by allowing for the comparison of common components within a BOM.
70. What is the Enterprise Resource Planning (ERP) model and why is it important for businesses?
The ERP model is a system used by businesses to manage resources such as manpower, materials, machinery, money, method, and time efficiently.
It helps companies grow rapidly by utilizing these resources to run their day-to-day business processes. ERP systems like SAP, Oracle, PeopleSoft, Jerry Edwards, Bon, Microsoft Dynamics, and Ramco are available in the market.
71. What is the goal of implementing an ERP system in a business?
The goal of implementing an ERP system in a business is to increase productivity, reduce production costs, improve system performance, and ensure customer satisfaction.
72. What is SAP and what models does it offer?
SAP is a leader in the ERP environment, with a history dating back to 197It is based in Germany and offers various models, including technical and functional models.
Technical models include advanced business application programming, business administration, system and degree resolution, and other modules like BABW, business intelligence, XPA, exchange infrastructure, and master data management.
73. What background is required to learn the technical models of SAP?
A background in the IT industry or knowledge of IT skill site technologies is required to learn the technical models of SAP.
74. What are functional modules in SAP and who are they suitable for?
Functional modules are essential components of a company’s operations, dividing departments into subcategories.
They are suitable for individuals with non-faction or industrial experience, such as those in pharmaceutical, chemical, automobile, mechanical, or retail industries.
The SAP model does not require any software skills or knowledge. Some functional modules require domain experience, while others require initial experience to understand the business process.
75. What is the difference between creating a production order in the real world and in SAP?
Creating a production order in the real world requires an understanding of the total business process and the reasons behind it. In SAP, a production planning engineer knows the tasks, operations, and activities, but the difference is how they are framed in the SAP environment.
76. What are base functional modules in SAP and who should use them?
Base functional modules are mandatory for any client business, regardless of the nature of the business.
77. What are advanced functional modules in SAP and who should use them?
Advanced functional modules, such as supplier relationship management (SRM), customer relationship management (CRM), and business processing consolidation (BPC), are recommended for those with a background in business management, sales and distribution, or MMP.
78. What industry-specific products require certain functional modules in SAP?
Industry-specific products, such as IS retail, oil and gas, utilities, healthcare, automotive, pharmaceutical, media, banking, and railways, require certain mandatory functional modules.
These modules are essential for those interested in implementing and recommending these modules to their clients.
To sum up, SAP Production Planning, or SAP PP (Production Planning), is an essential module in the SAP ERP system that aids companies in effectively managing their production operations. Ace more knowledge by learning SAP PP interview questions with answers pdf.
To assure customer satisfaction and streamline production activities, it provides a range of functionalities such as inventory management, order management, production planning, and reporting.
With its cutting-edge capabilities, including explosive analysis, bill of material management, and connectivity with other SAP modules, SAP PP is a crucial tool for companies trying to streamline their operations and cut expenses.
If you work in the manufacturing sector or a similar field, knowing the fundamentals of SAP PP will help you make better decisions and boost productivity within your company.
I hope your next interview goes well.
All the Best!!!
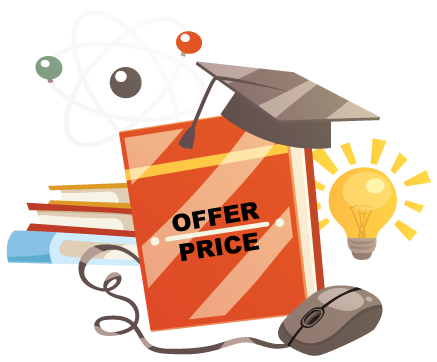
SAP PP Course Price
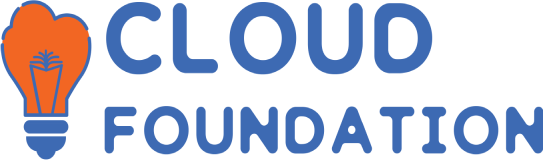
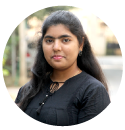
Saniya
Author