SAP PM Interview Questions
SAP PM Interview Questions!!! Are You Nervous for an SAP PM Interview? Don’t worry! With adequate preparation and mindset, any question posed during an SAP PM interview should not be too difficult for you to answer.
Remember, this is a chance to demonstrate your experience and enthusiasm for the SAP PM module!
As part of this SAP PM module interview questions and answersblog, we provide a comprehensive approach on interview preparation.
This resource covers everything, from frequent interview questions and helpful advice to common interview blunders.
When reviewing these resources, bear in mind that an ideal applicant profile includes proficiency, passion, problem-solving ability, and critical thinking skills.
SAP PM Interview Questions and Answers:
1. What is the role of the bomb bill of material in understanding an organization’s operations?
The bomb bill of material provides crucial information about the structure of equipment, including spare parts. This information is essential for understanding the organization’s operations and the use of equipment.
2. What is the difference between a maintenance plan and a planning plan?
A maintenance plan is a location or site where equipment and machines are located, while a planning plan is a location or site where people sit and perform planning activities.
3. What are the different categories of bombs in SAP?
The different categories of bombs include equipment, functional location, assembly, and material bombs.
4. What is the role of the box sector in maintenance activities?
The box sector is a group of technicians responsible for maintaining and repairing equipment.
5. What is the significance of master data in managing equipment within an organization?
Master data is crucial for managing and optimizing resources and operations within an organization by understanding different types of tasks, data, and classifications.
6. What is the significance of understanding the architecture of SAP?
Understanding the architecture of SAP is essential for logging on and accessing transactions in the system.
7. What is the role of the work center in maintenance activities?
The work center is the person responsible for maintenance activities, and the data maintained in the work center helps determine where it is assigned.
8. What are the different types of task lists in the plan maintenance model?
The different types of task lists include equipment, general, and communication task lists.
9. What are the three main steps involved in the maintenance process?
The three main steps involved in the maintenance process are regular maintenance, breakdown maintenance, and preventive maintenance.
10. What happens during the regular maintenance process?
During regular maintenance, a production department observes a machine with a problem and notifies the engineering department, who create a work order for the repair activity.
The technician then performs the repair using necessary materials and spare parts from the warehouse, and the maintenance planner or supervisor completes and confirms the order.
11. What is the difference between breakdown maintenance and regular maintenance?
Breakdown maintenance occurs when a machine completely stops due to a total breakdown, and the production department informs the engineering department through a different type of notification to create a work order for the repair activity.
12. What are the three types of preventive maintenance?
The three types of preventive maintenance are time-based, performance-based, and condition-based.
13. What is time-based preventive maintenance?
Time-based preventive maintenance involves cleaning the machine, opening it, applying oil, or changing critical parts based on a specific time interval.
14. What is performance-based preventive maintenance?
Performance-based preventive maintenance involves determining when to perform certain maintenance activities based on the performance of the machine or equipment.
15. What is condition-based preventive maintenance?
Condition-based preventive maintenance involves setting up the system to automatically generate orders when specific machine conditions, such as temperature, pressure, or thickness, are not met.
16. What role does master data play in maintenance management?
Master data is essential for successful maintenance management as it provides important information about the equipment and machines, including their classification and configuration.
17. How can businesses streamline their maintenance operations?
By setting up a system that automatically generates orders once a specific time or counter-graduation is reached, businesses can streamline their maintenance operations and ensure the smooth functioning of their machinery.
18. What is the role of the maintenance strategy in industry?
The maintenance strategy is crucial in industry for creating plants and scheduling preventive maintenance activities to reduce the need for purchasing new spare parts. It includes the refurbishment of spare parts through the test equipment management (TEM) function.
19. What is the Test Equipment Management (TEM) function, and how does it integrate with other modules?
The TEM is a preventive maintenance function that checks the quality of materials and calibrates them periodically. It integrates with QMOD, PM, and QM modules to ensure the accuracy and reliability of test equipment data.
20. What is the investment auto process used for in maintenance management?
The investment auto process is used for managing new input queue missions where organizations need labor, manpower, and spare parts when procuring new machines or equipment.
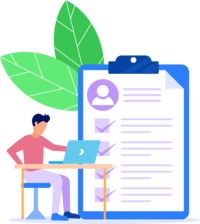
SAP PM Training
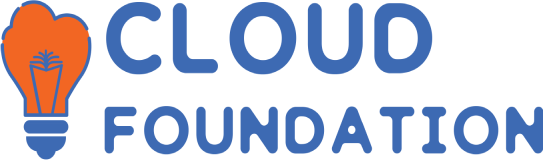
21. What types of reports are generated in the plan maintenance model?
The plan maintenance model includes standard, analytical, master, transactional, and miscellaneous reports, as well as PMAS reports, plan maintenance information system reports, and miscellaneous reports for generating and analyzing data.
22. What we are going to learn in SAP PM module?
In SAP PM module include the theory of data migration to LTFC, the use of the ref plus business rule framework plus, and minor changes from CD C to S4 100 with respect to PMConfiguration, including front end and back-end configurations of mass-related technical objects, maintenance configuration, and regular maintenance, is also discussed.
23. How does the SAP PM module integrate with other modules?
The SAP PM module integrates with other modules such as purchasing, inventory management, and PB through touch points and the integration process to facilitate efficient maintenance activities.
24. What are the key functions of the SAP PM module?
The key functions of the SAP PM module include repairs, inspections, and preventive maintenance for maintaining high availability of the technical system.
Repairs are used for addressing breakdowns, inspections check the actual condition, and preventive maintenance is used for proactive maintenance activities.
25. What is the importance of structuring an organization according to a technical system in maintenance activities?
Organizations must structure their maintenance activities according to a technical system by dividing the existing maintenance structure into technical objects to define machine types. This allows for efficient management and organization of maintenance activities.
26. What are the three types of technical objects?
Technical objects can be divided into three types: functional structuring, object-based structuring, and functional and object-based structuring.
Functional structuring divides the technical system into professional locations, object-based structuring divides the technical system into pieces known as equipment, and functional and object-based structuring combines both approaches.
27. What is the role of work centers in creating functional structures and equipment?
Creating a functional structure, functional location, and equipment requires a work center. In the next tutorial, the process of creating a work center and functional locations or equipment for the plant maintenance module will be demonstrated.
28. What are permits, and how are they used in maintenance activities?
Permits are mass data used to ensure compliance with health and safety regulations and control maintenance order processing. They are used in two ways: technical permits and classified and process-oriented permits.
Technical permits define rules or conditions to be observed during the execution of maintenance tasks, and they must be granted before an order is released. Once permits are maintained, they are assigned to the technical objects, which are functional locations and equipment.
29. What is the purpose of using permits during order processing?
The purpose of using permits during order processing is to ensure that necessary safety proposals are taken and that the work has been approved at the management level.
30. How can a permit be created using the transaction code IPMD?
To create a permit using the transaction code IPMD, the user first creates a hard work permit and then a work permit. These permits are assigned to the technical objects, such as functional location or equipment.
The user then creates a maintenance order using the transaction code IW31 and assigns the permits to the necessary technical objects.
31. What information does the system display when checking equipment for permits?
The system checks whether the equipment is under warranty and displays the type of permits used.
32. What action can the user take when encountering an issue with the automatic release failed option?
The user can go to transaction code IPM2 to display the list of permits for approval, activate the indicator “not issued issued,” and enter the order to allow execution of the permit.
33. What message is displayed when the permits are created and assigned to the equipment?
The system displays the message “maintenance order will be released after update.”
34. What is the process for creating a process-oriented permit?
To create a permit, use transaction code CT04 and plan the cost, which can be any amount. The cost is saved in the system under the field name CSev_permit, stored in the table CSev_permit.
35. What is the next step after creating a permit?
Create a class with multiple characteristics using transaction code CL0. Assign the characteristic value to the desired level and create new entries for each level, including level 1 description, level 2 approval category, and order lists for print not modifiable. Repeat this process for levels 3 and 4.
36. What is the process for deleting previous permits and creating a new order for processor entered permits?
Enter the equipment number and select permits from the menu bar to delete previous permits. Create a new order for processor entered permits and enter the order type priority by equipment.
The system displays whether the equipment is on the warranty or not, and enter the description and cost in the header data.
37. Why is it important to effectively manage permits?
Effectively managing permits ensures their accuracy and efficiency during maintenance processing.
38. What information is included in the master data for equipment permits?
The master data for equipment permits includes work center function location, equipment serial number, equipment bomb function location, assembly bomb, material bomb classification, permits, catalogs, measuring points, measuring counters, and revision.
39. Where can you view the equipment master data?
The equipment master data can be viewed in IE02 equipment, which includes the structure, class, characteristics, serialization, permits, and division. Additionally, there is a measuring partner, working center, and work center master data.
40. What is the process for starting the maintenance executions notification?
Once the master data is completed, the maintenance executions notification process takes two weeks to complete. After completing the master data, maintenance orders can be executed on the equipment.
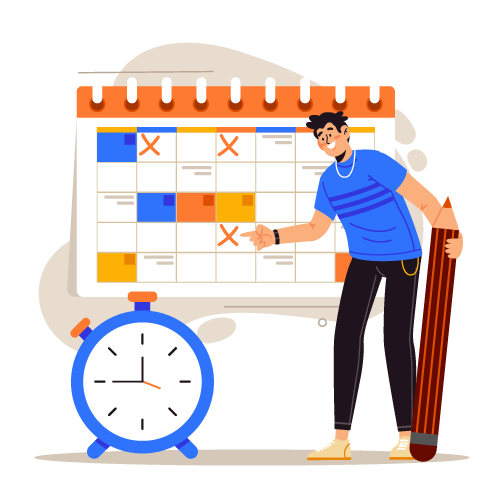
SAP PM Training
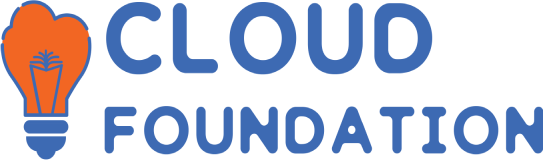
Let’s keep more interactive with SAP PM in the form of MCQ’S
1. What is the role of the bomb bill of material in the plan maintenance model?
A) It provides information about the organization’s functional locations
B) It provides information about the structure of equipment, including spare parts
C) It is responsible for performing preventive maintenance activities
D) It determines the work center responsible for maintenance activities
2. Which group of technicians is responsible for maintaining and repairing equipment?
A) The task list
B) The box sector
C) The work center
D) The master data
3. What is the purpose of creating and using task lists in the plan maintenance model?
A) To group equipment and functional locations
B) To perform preventive maintenance activities
C) To provide information about the structure of equipment
D) To determine the classification of equipment
4. What is master data in the context of managing and optimizing resources and operations in the plan maintenance model?
A) Data related to the different types of equipment classifications
B) Data related to the different types of tasks and their classification
C) Data related to the organization’s functional locations
D) Data related to the structure of equipment and spare parts
5. What is the purpose of master data revision in the context of plant operations and maintenance tasks?
A) It is a temporary shutdown of a plant or location for performing preventive maintenance tasks
B) It is a process for managing and optimizing resources and operations in the plan maintenance model
C) It is used to capture the configuration settings for maintenance orders
D) It is a period of time when equipment is in operation and collecting measurable data
6. How is a revision created in the system?
A) By selecting the revision number and entering the start and end dates
B) By creating a new entry in the planning plant and entering the revision number
C) By activating the release division completed for a specific revision
D) By viewing all the orders created under the revision using the transaction code IW39
7. What information is captured when creating a revision in the system?
A) The configuration settings for the revision number
B) The start and end dates for the revision period
C) The equipment data, including start and end dates and revision days
D) The cost for creating a maintenance order for a specific equipment
8. Which transaction code is used to view all the orders created during a specific revision?
A) YOB
B) IW39
C) SPRBO
D) SPRF
9. What are measuring points and measuring counters used for in a plant maintenance model?
A) To describe physical or logical locations at which a condition is described
B) To indicate the classification of equipment
C) To determine the work center responsible for maintenance activities
D) To perform preventive maintenance tasks
10. Which master data item is the first to be added in a plant maintenance system?
A) Work center
B) Measuring point
C) Characteristics
D) Serial number
To sum up, SAP PM, also known as SAP Plant Maintenance, is an effective enterprise resource planning (ERP) tool designed to assist businesses in organizing and managing their maintenance processes.
SAP PM integrates work order management, inventory planning, preventative maintenance, and other maintenance management functions to help firms minimize downtime, increase productivity, and streamline operations.
Because of its extensive capability, scalability, and flexibility, SAP PM has grown in popularity among businesses looking to improve their maintenance procedures and get a competitive advantage.
I hope you will crack your next interview.
All the Best!!!
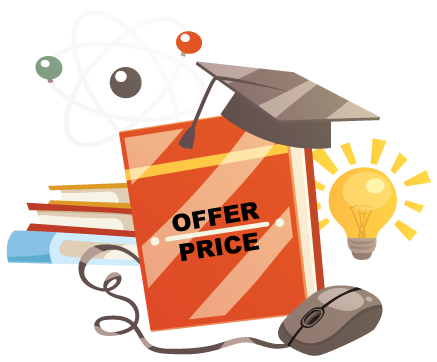
SAP PM Course Price
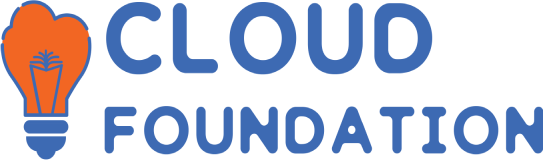
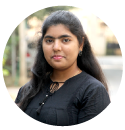
Saniya
Author