Lean Training | Learn Lean Course
About Lean
The original Lean business strategy was born out of Toyota’s Japanese manufacturing philosophy, which prioritizes the elimination of waste, the enhancement of the customer experience, and the pursuit of continuous improvement. The concept has expanded beyond its initial use in manufacturing to improve efficiency, productivity, and competitiveness in a variety of industries.
The core principle of Lean is to identify what the consumer needs and provide them with only those features that meet their needs. By breaking down the process into its component parts, Lean may help you find inefficiencies and eliminate them, allowing you to work without interruptions.
Embracing a Lean mindset promotes a spirit of cooperation, teamwork, and constant progress. Important ideas in Lean include value establishment, value stream mapping, flow creation, pulling, and perfection. With Lean, businesses can respond more quickly to shifts in the market and in consumer demand.
To enhance productivity, quality, and organizational performance, it is essential to engage people, provide learning and development opportunities, and eliminate waste on a continual basis.
Lean principles provide a framework for contemporary businesses to increase growth, innovation, and competitiveness by helping them maximize customer value while minimizing waste and inefficiency.
Benefits of Lean
Implementing Lean techniques into an organization may bring several benefits both for itself and for its consumers. Here are a few major ones.
Enhance Efficiency and Productivity: Lean methods utilize optimized workflows and waste elimination strategies, leading to more productive operations that may include reduced lead times, shorter cycle times, or increased productivity. This may result in shorter lead times or lower cycle times that lead to faster delivery times or increased productivity levels.
Improved Quality: Lean promotes improved product and service quality by eliminating flaws and prioritizing continuous improvements, leading to higher customer satisfaction and loyalty.
Increased Flexibility: Lean firms benefit from being equipped with simplified processes and an ongoing improvement culture that help them adapt more easily to changing market circumstances and consumer requirements.
Cost Savings: By eliminating waste and improving processes, Lean can help firms lower costs and become more cost competitive in the marketplace.
Empowered Workers: Lean promotes cooperation and collaboration, giving workers more feeling of ownership over their work and control of it, leading to higher engagement, work satisfaction, and motivation levels.
Increased Customer Satisfaction: Lean’s emphasis on providing value to customers and continuously improving processes may result in higher levels of customer satisfaction as firms more effectively meet customers’ requirements and expectations.
Increased Competitivity: Lean can help firms remain market competitive by improving efficiency, productivity and quality in ways that increase efficiency, productivity and quality; it may even give an advantage over their competition in certain situations.
Continuous Improvement: Lean is not a one-and-done affair — rather it should be seen as an ongoing activity within an organization’s culture of continuous improvement, in order to stay ahead of competition while adapting to changing market circumstances and consumer expectations.
Sustainability: Lean’s focus on waste reduction and process improvements may help firms maximize resources while decreasing environmental impacts.
Prerequisites of Lean
While various requirements exist to achieve successful Lean transformation, I will highlight five essential ones for every firm beginning their journey along this road.
Leadership Support: For any successful Lean transformation to take place, having strong and committed leaders who embrace and believe in Lean is absolutely crucial.
They should inspire their teams with Lean concepts while offering them resources necessary for smooth implementation of this transition process.
Cultural Readiness: Lean requires an organization-wide shift, so it’s vital that its culture is prepared for such an endeavour.
This could involve building an atmosphere of continual improvement, trust and cooperation within your workforce – encouraging new ideas while working in multifunctional teams collaboratively on cross-functional tasks and communicating openly and honestly amongst colleagues.
Training and Education: For any successful Lean training transition to take place, proper employee education and training is vitally important.
Employees need the ability to identify wasteful practices, streamline processes and collaborate effectively – which means training programs must meet each company’s particular requirements and their workforce accordingly.
Set Clear Goals: Setting clear and well-defined goals is integral to the successful transitioning to Lean.
Organizations should set project-related objectives such as decreasing lead times, improving productivity or increasing quality that align with their strategic goals and are quantifiable in nature.
Data-Driven Decision Making: Lean utilizes data to uncover waste, optimize processes and make sound choices. Therefore, organizations need the ability to efficiently collect and analyze their own data in support of Lean initiatives – this may require investing in analytics software as well as creating an environment conducive to data-driven culture.
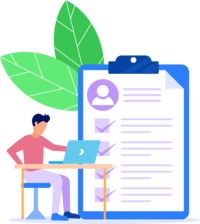
Lean Training
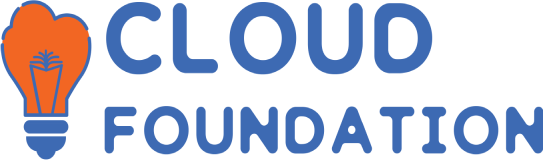
Lean Lean Tutorial
Lean Management: Delivering Value, Eliminating Waste and Continuously Improving
Lean management has quickly gained prominence within business circles due to its simplicity: value creation from customer viewpoint, waste elimination and continuous improvement.
Even though it may seem daunting at first, this strategy may make your argumentative writing assignment more persuasive by providing evidence that is both brief and compelling.
Lean Methodology: Understanding and Applying the Principles
Lean methodology relies on three central ideas: providing value from a customer-first viewpoint, eliminating wasteful processes, and continuously improving.
Beginners to Lean management can gain a better grasp of its principles and applications across industries by understanding its core idea, or “Lean management”, at first hand.
Lean is an approach focused on continually optimizing work processes, purposes and people for maximum effectiveness and improvement.
Originating in Toyota production system, Lean production aims to decrease processes that do not add any added value to their end products.
Lean thinking has proven its success across various industries and evolved into five basic principles for implementation.
Lean Principles and Value-Driven Processes
To implement Lean practices effectively, companies need to understand what value their customer demands they provide – this helps identify waste as well as processes which don’t add any real benefit.
Continuous Team Collaboration To facilitate smooth team collaboration
The second principle involves developing a continuous workflow by breaking work into smaller batches and visualizing its progress. Doing this allows process roadblocks to be identified quickly and removed easily.
Creating a Pull System for Faster Task Delivery in Lean Management
Lean Management Recommends Establishing a Pull System to Deliver Tasks More Rapidly Lean management advocates creating a pull system so teams can complete their work faster with reduced effort, observations and continuous improvement efforts.
This fourth principle has since shaped Lean management’s evolution over the years.
Lean management is an approach devoted to optimizing every facet of work processes at every level in an organisation’s hierarchy, offering several advantages including enhanced productivity and efficiency, intelligent processes, more resourceful use and stable production system management.
Lean principles aim to maximize resource use while including all employees in their improvement process for maximum customer value creation.
Six Sigma Fundamentals: Deliberating Processes and Minimizing Variation
Six Sigma’s fundamental principles focus on identifying processes while taking into account various considerations including personnel, materials, machines and work environment methods.
A crucial aspect of quality characteristics for customers lies within using six-sigma tools to translate customer needs to tangible products or process requirements; such projects often fall within essential quality requirements cost of quality and delivery requirements as their focus areas.
The Importance of Customer, Business, and Employee Voices in Project Selection
Customer, business and employee voices all play an integral part of this process. Customers provide insights that assist project selection; while businesses use voice analysis to pinpoint market weaknesses such as capital usage/utilization status/process complexity.
Finally, employees’ voices help foster personal ownership/responsibility as they contribute directly to company’s success.
Eliminating Waste in the Workplace: The Eight Waste Points
Waste in the workplace can have significant costs and defects associated with its manufacturing processes, leading to substantial expenses and delays. Eight waste points have been identified: defects, overproduction, waiting time, non-utilized, transportation access for inventory accessing, motion access as well as access processing access.
Eliminating Waste in Production: A Guide for Improving Efficiency
Overproduction involves using raw materials or works-in-progress early or quicker to fulfil demand. Defective goods, services, or information may need rework, review, or retesting.
Clear operational norms, automated processes, and quality assurance are needed to eliminate waste. Waiting material or information involves planning, scheduling, system updates, and CRM/ERP software.
Transportation access is unnecessary product delivery of equipment or material transportation services, whereas untapped talent is any team member’s unused skills, talents, knowledge, or innovation.
Inventory access requires overstocking. Motion access includes keystrokes, walking, sorting, stacking, and searching. Access processing is any action that does not generate consumer value.
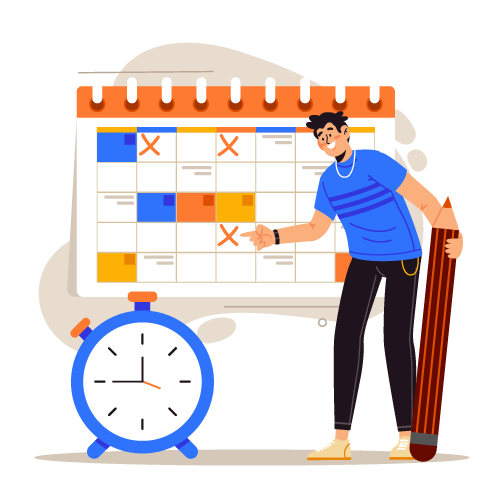
Lean Online Training
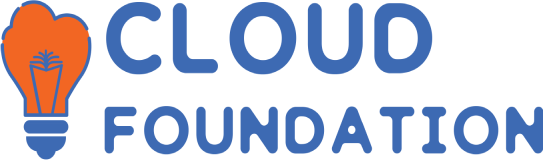
Modes of learning Lean
Lean Learning Methods Lean concepts and techniques reduce production waste while improving productivity, with self-paced and instructor-led live training serving as key Lean learning methodologies.
Instructor-Led Live Training: In order to get the most out of Lean, this approach suggests enrolling in a Lean online course run by certified Lean educators.
Real-time training allows participants to ask questions and offer feedback to an expert educator, who uses suggestions, explanations, and examples to help students comprehend subjects quickly and fully. Instructor-led Live Training is perfect for systematizing Lean since it is vibrant, dynamic, and engaging.
Self-Paced Training:Busy professionals and independent learners may study Lean course at their own speed and schedule with e-Learning. Video lectures, interactive simulations, quizzes, and assessments allow students to review topics at their own pace and serve Lean veterans who want refresher courses or specific tools and approaches.
Both Lean learning approaches have pros, therefore the choice depends on personal preferences and circumstances. Live instructor-led training gives interaction, guidance, and organized progress, while self-paced learning allows flexibility and advancement at your own speed.
Lean Certification
There are different levels of Lean certifications, such as white belt, yellow belt and green belt.
White Belts: White belts work closely with higher-tier individuals to explain basic principles associated with 6 Sigma and its processes.
Yellow belts: Yellow belts acquire knowledge about the fundamentals of DMC and how its disciplines may be implemented into workplace environments.
Green Belts: Green belts help a 6 Sigma black belt by analysing and solving quality problems independently, often leading and managing projects independently. Green belts have in-depth knowledge of 6 Sigma methods and procedures which they bring to bear on any business they support.
Black Belt Certification for Lean Six Sigma
Lean Six Sigma black belt certification is an esteemed achievement awarded to professionals who possess in-depth knowledge of DMAIC Model 6 Sigma principles and practices, acting as agents of change within organizations while leading their teams effectively using team leadership techniques as they enact change according to 6 Sigma principles.
Finally, Lean online training teaches us an ingenious technique that blends principles from Lean Manufacturing with Information Technology in order to eliminate inefficiency, enhance effectiveness, and maximize productivity.
Lean Technology empowers organizations to increase customer value and continuous improvement, streamlining processes while decreasing lead times and improving flexibility.
This approach elevates IT projects to new heights by seamlessly incorporating technology solutions with business strategy to produce an agile and nimble organization.
Implementation of Lean Technology allows businesses to increase their competitive edge while providing customers with superior products and services.
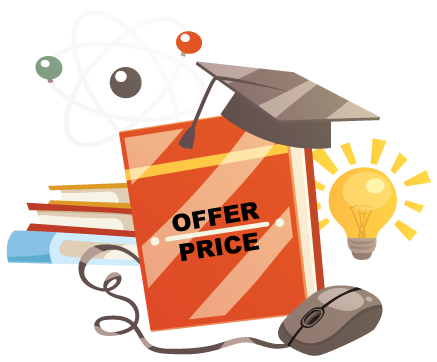
Lean Course Price
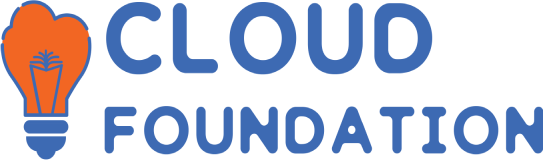
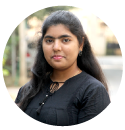
Saniya
Author